This is a great collaboration story. I worked with leaders of both Electrolux and Sears to develop the design language for the Kenmore Pro line. I guided alignment on a new platform variant to work for two brands and two companies.
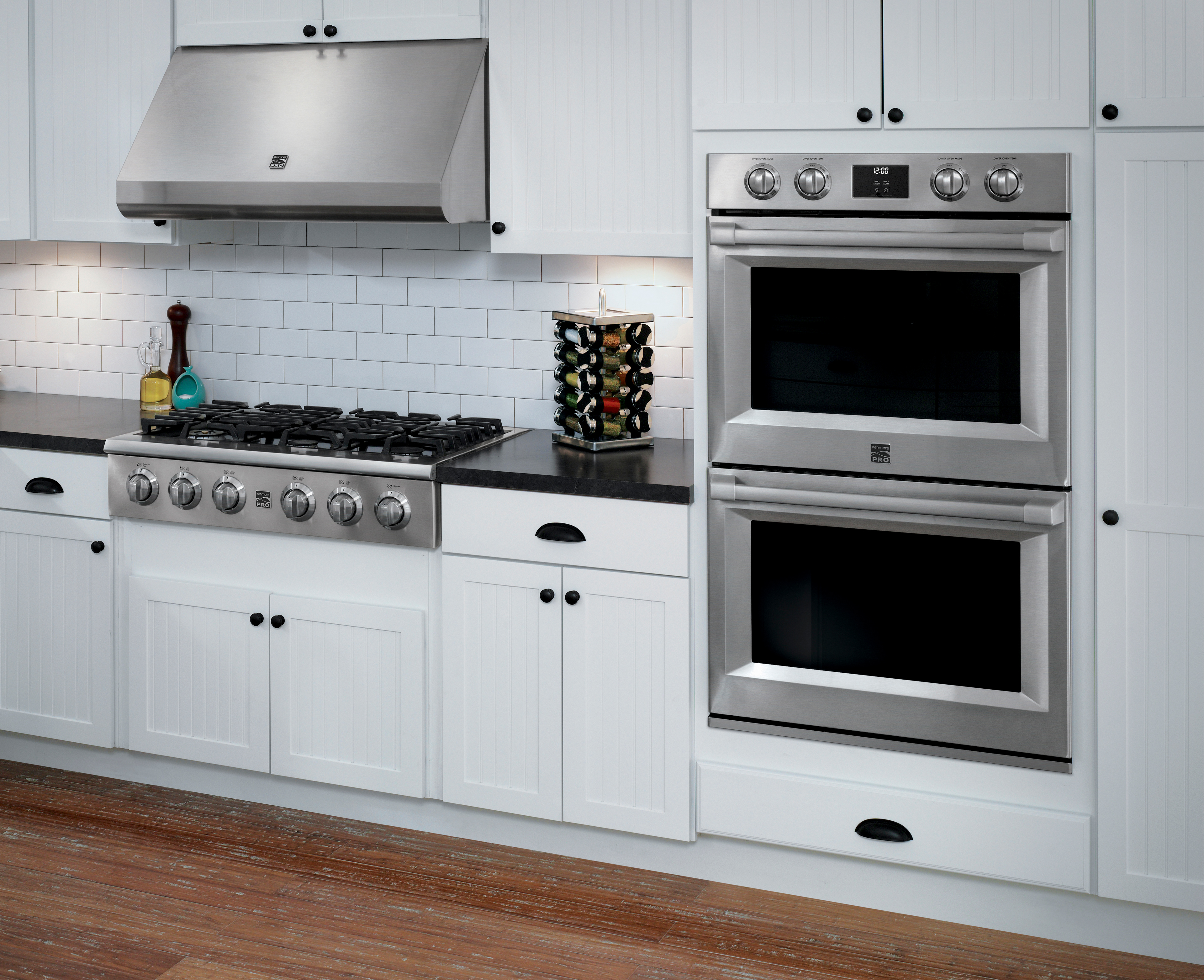
Electrolux was already committed to a professional style program when Kenmore came forward with their request for a new pro line. I had to balance the needs of both brands with just one platform. It was essential to both businesses that the two brands had distinct differentiation, yet there was a reluctance to put too much capital into the unique components. Part of the job of the designer in a project like this is to help illustrate what the essential parts are that need to be in scope, and how to commonize as much as possible.
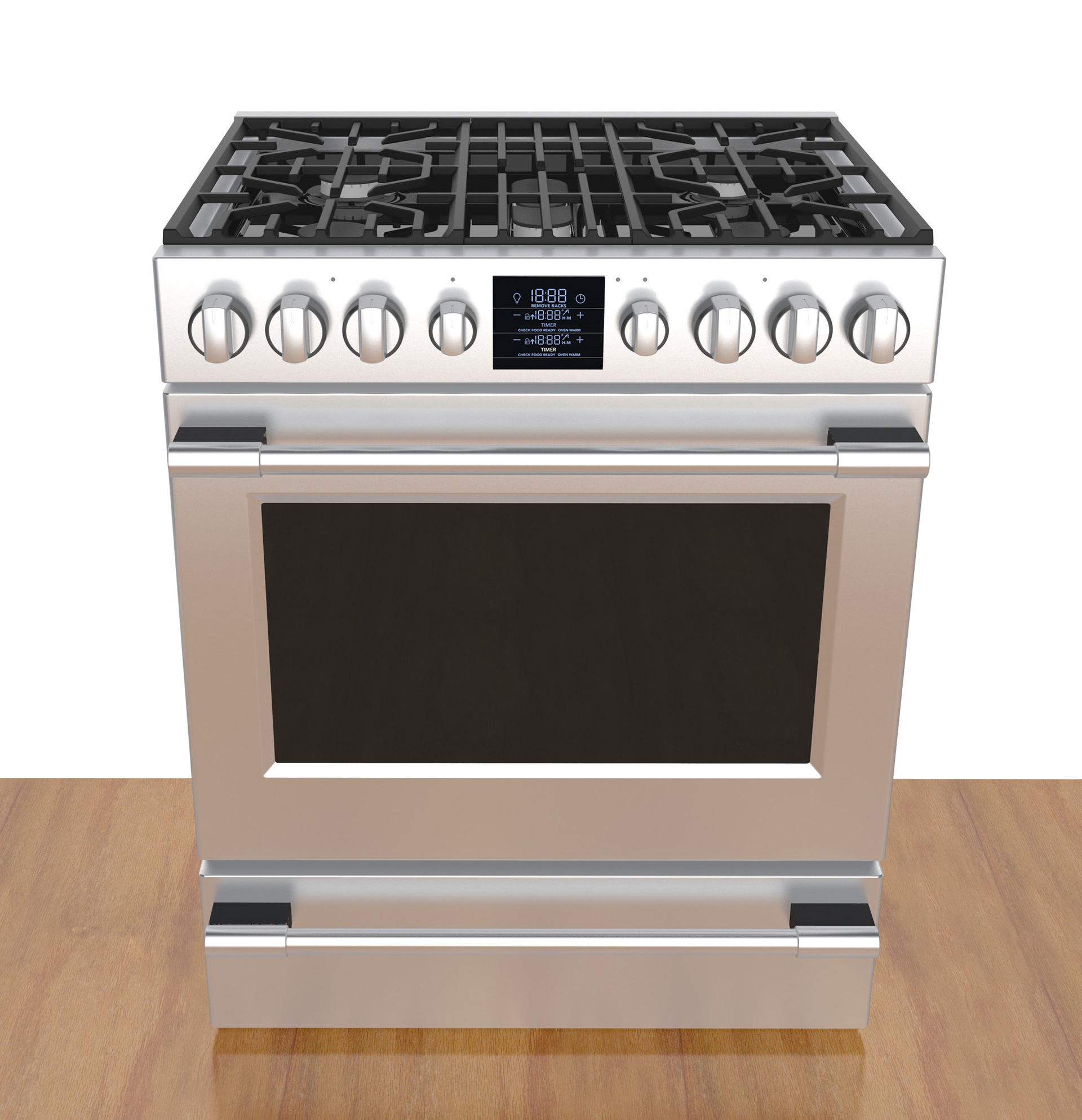
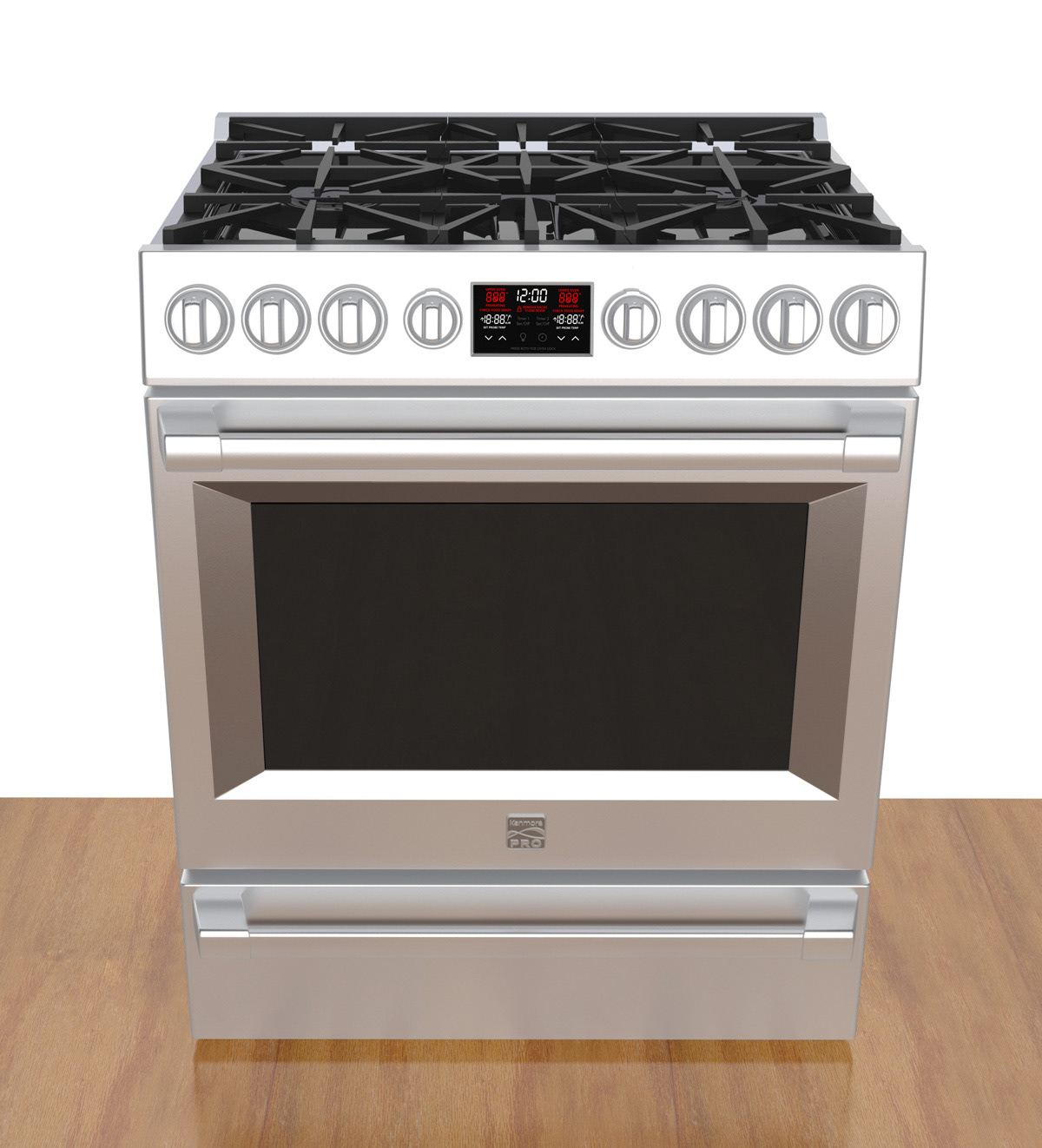
Kenmore provided a good download for their vision of the product. I was tasked to take their vision and iterate based on the brand values presented by the Kenmore team. Knobs, handles, and grates are always a given on a big design project for appliances, so I began to sketch on those parts with an emphasis on making the product feel professional.
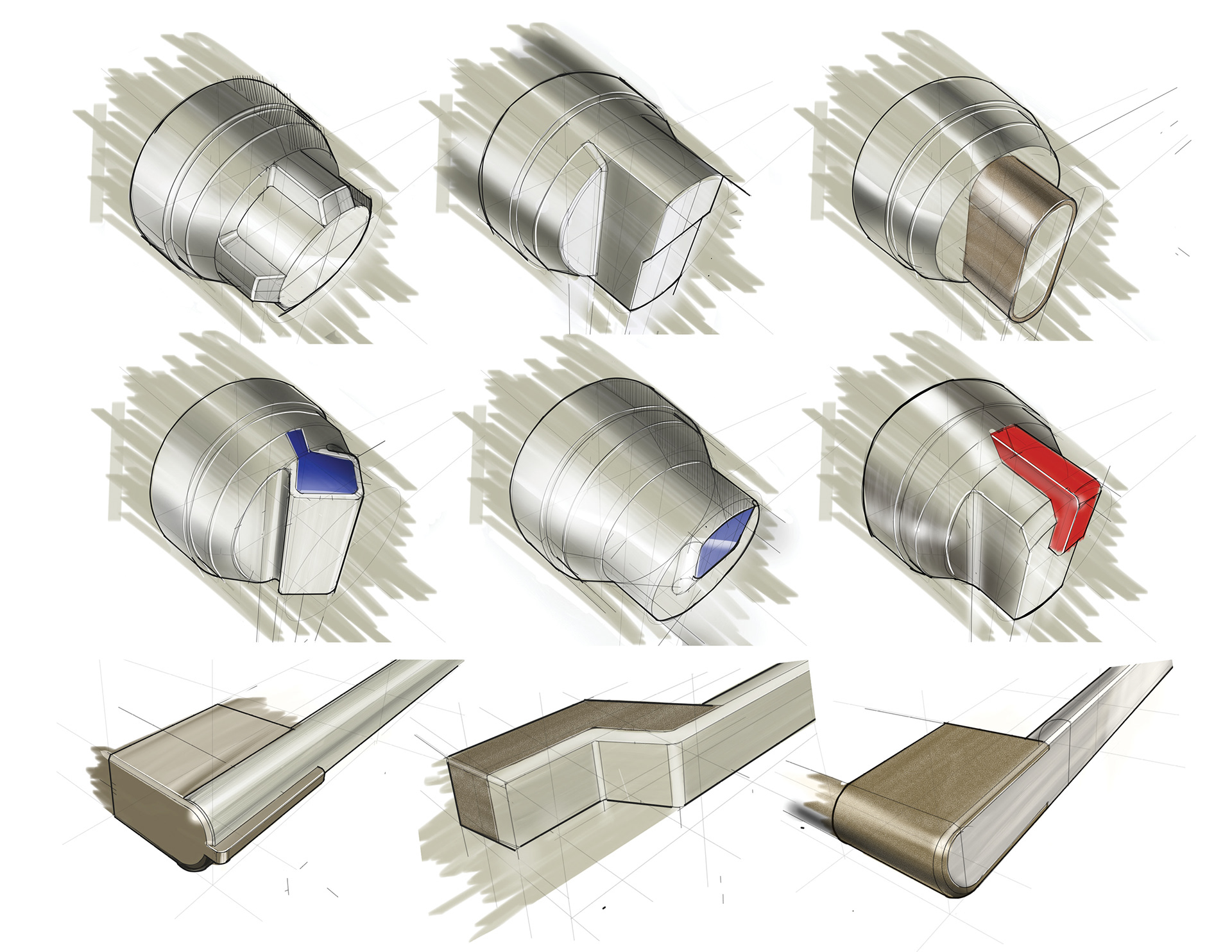
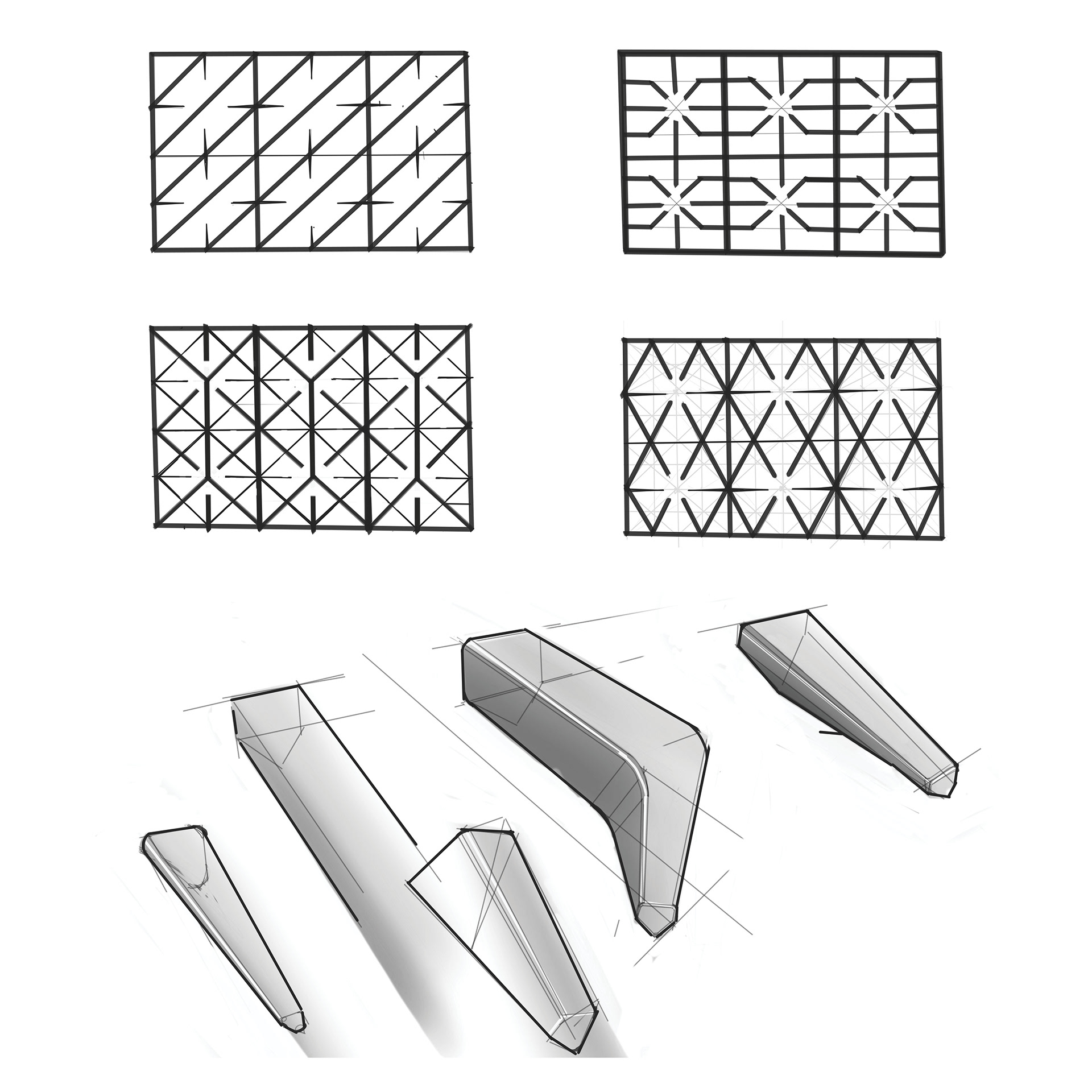
Prototyping is a key part of the design process. We used this base to try different parts to get a real feel of the proportions and look of the product. We used these to validate the next round of high-fidelity models.
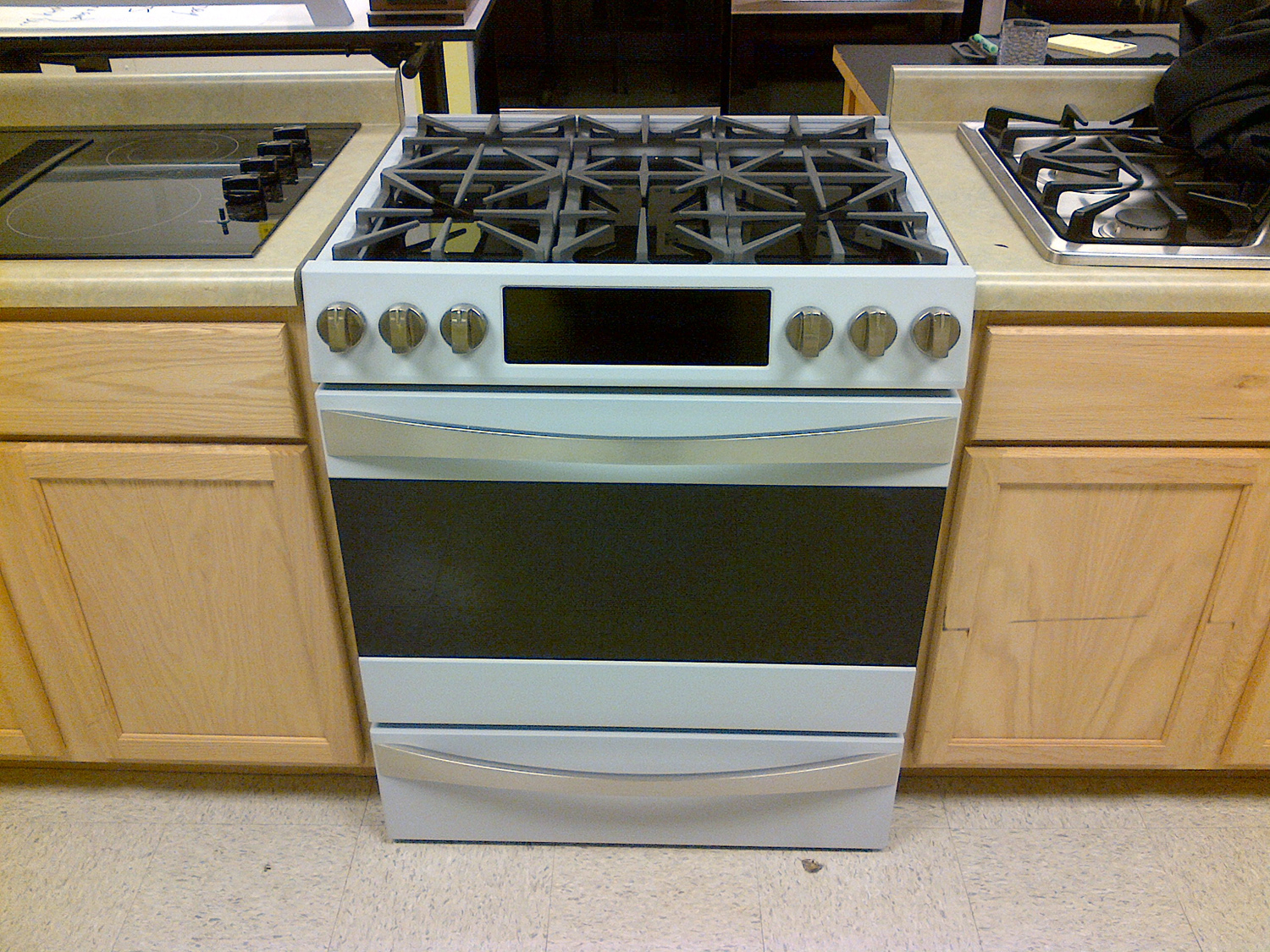
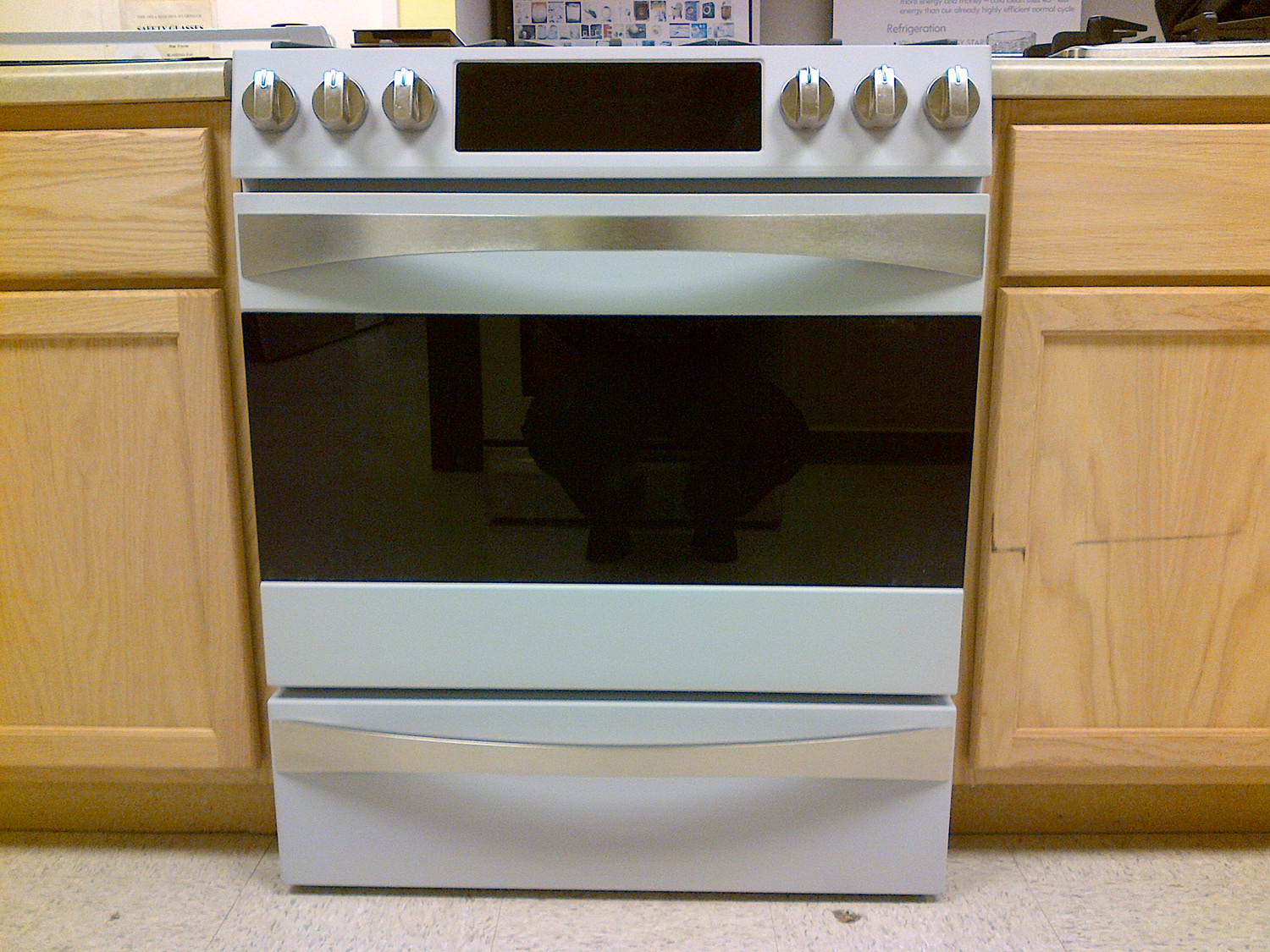
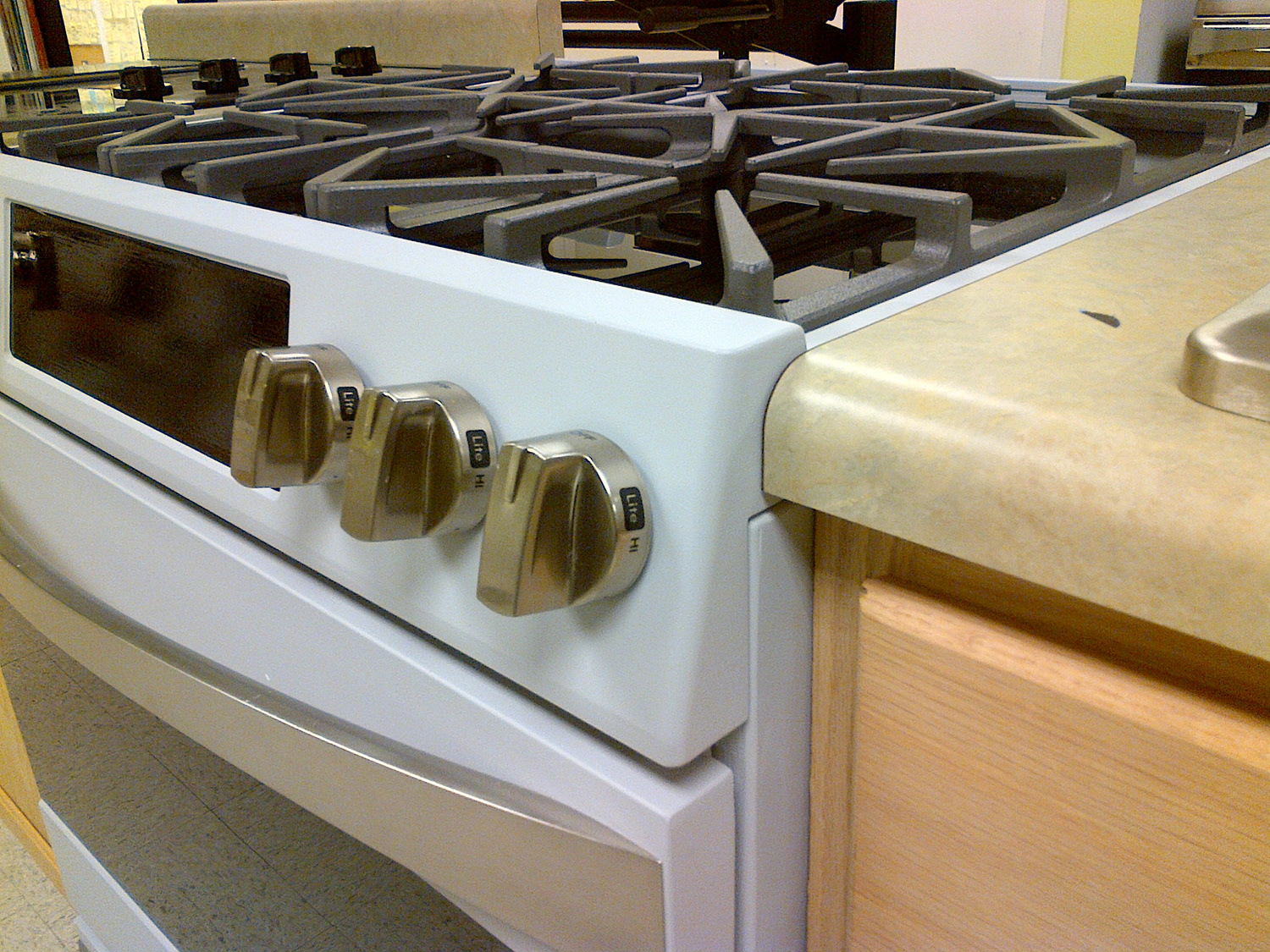
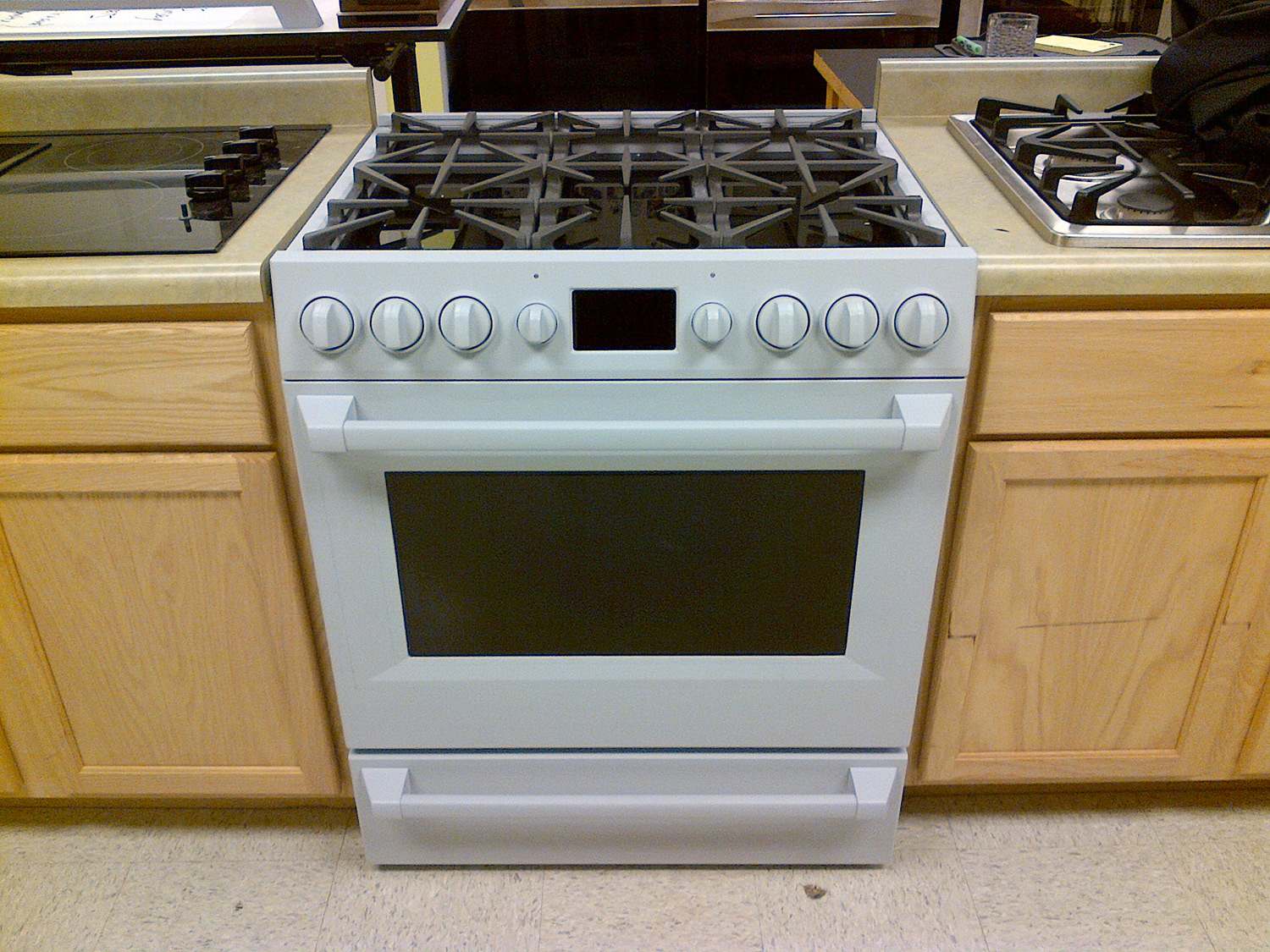
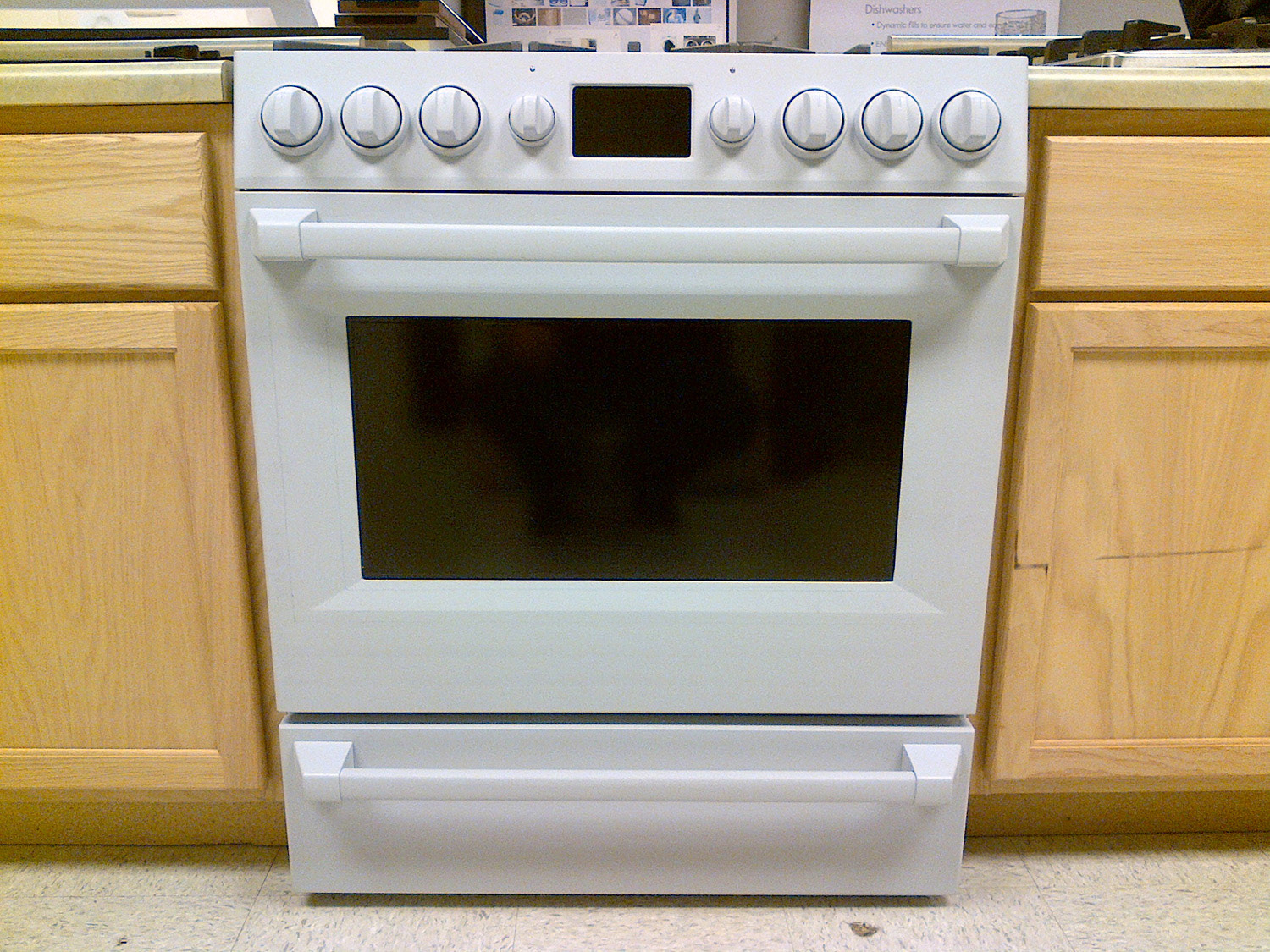
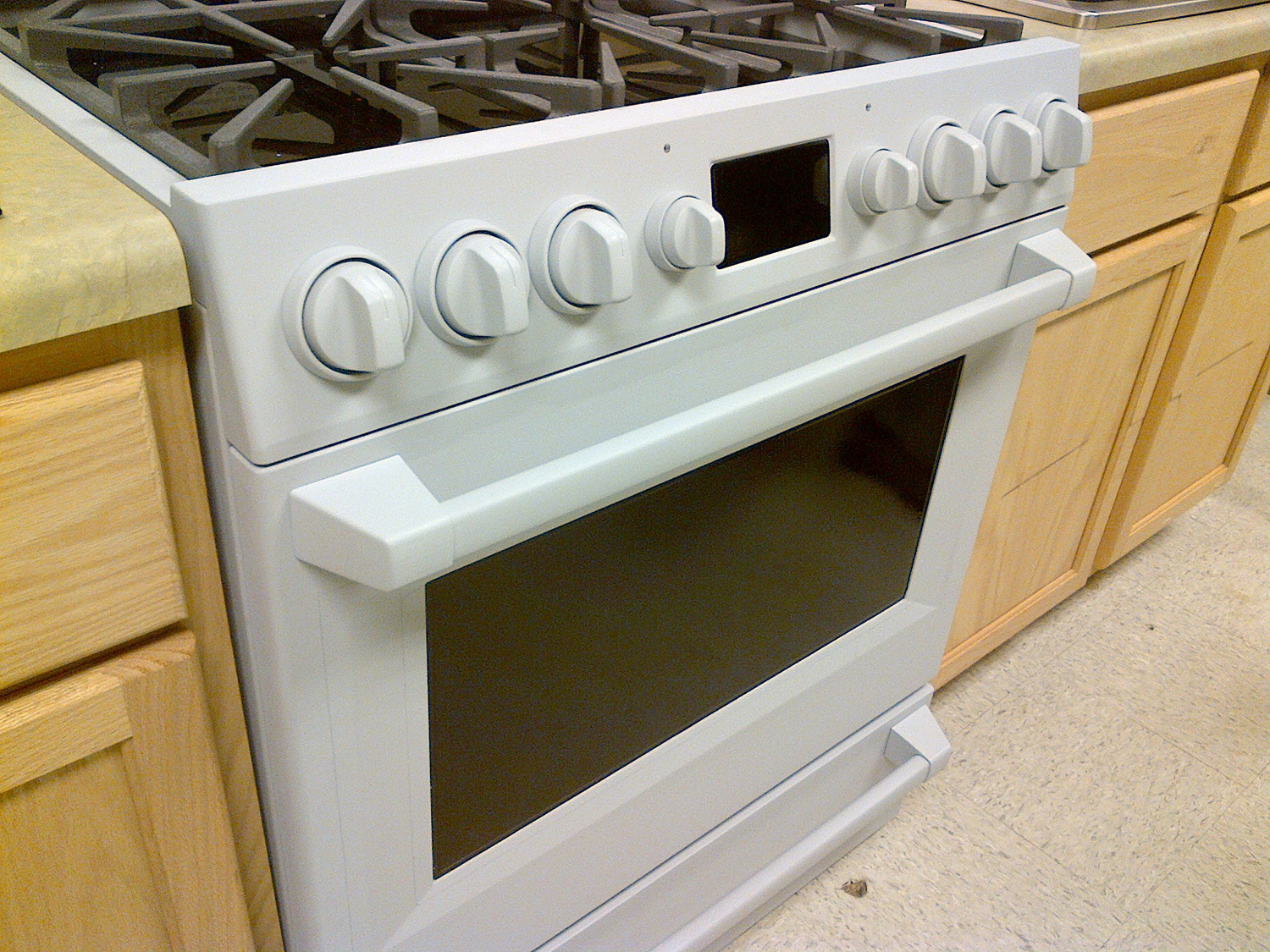
Grates are the focal point of a gas cooking product, and this was going to be the flagship model of the lineup. I put great emphasis on crafting the finger surfaces to personify 'pro.' A requirement for cooking ovens is that they need to vent. The challenge for this product is that the vents were right on the cooktop and highly visible. By designing the grate to incorporate the vent cover, we were able to minimize the visual impact of the vent holes.
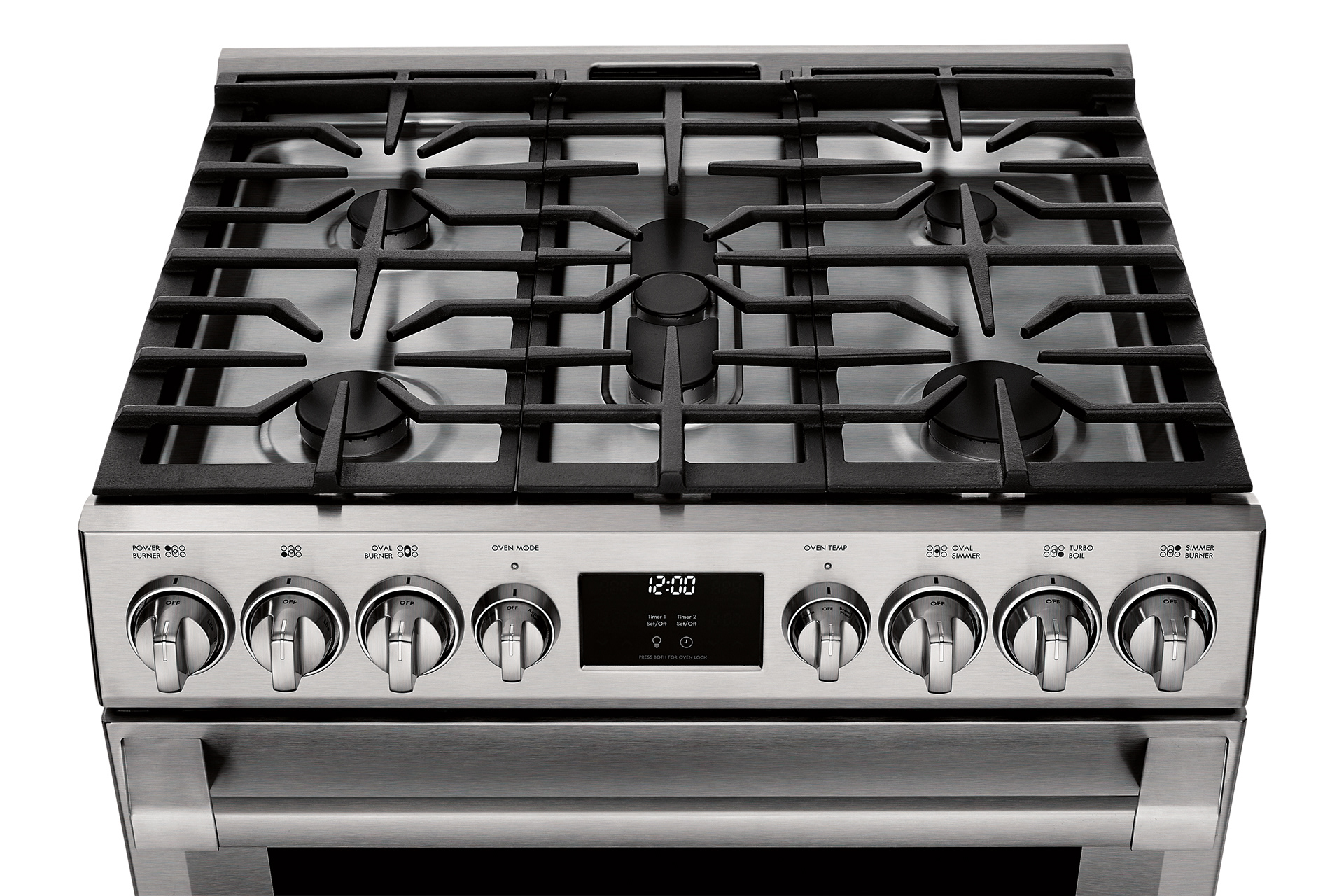
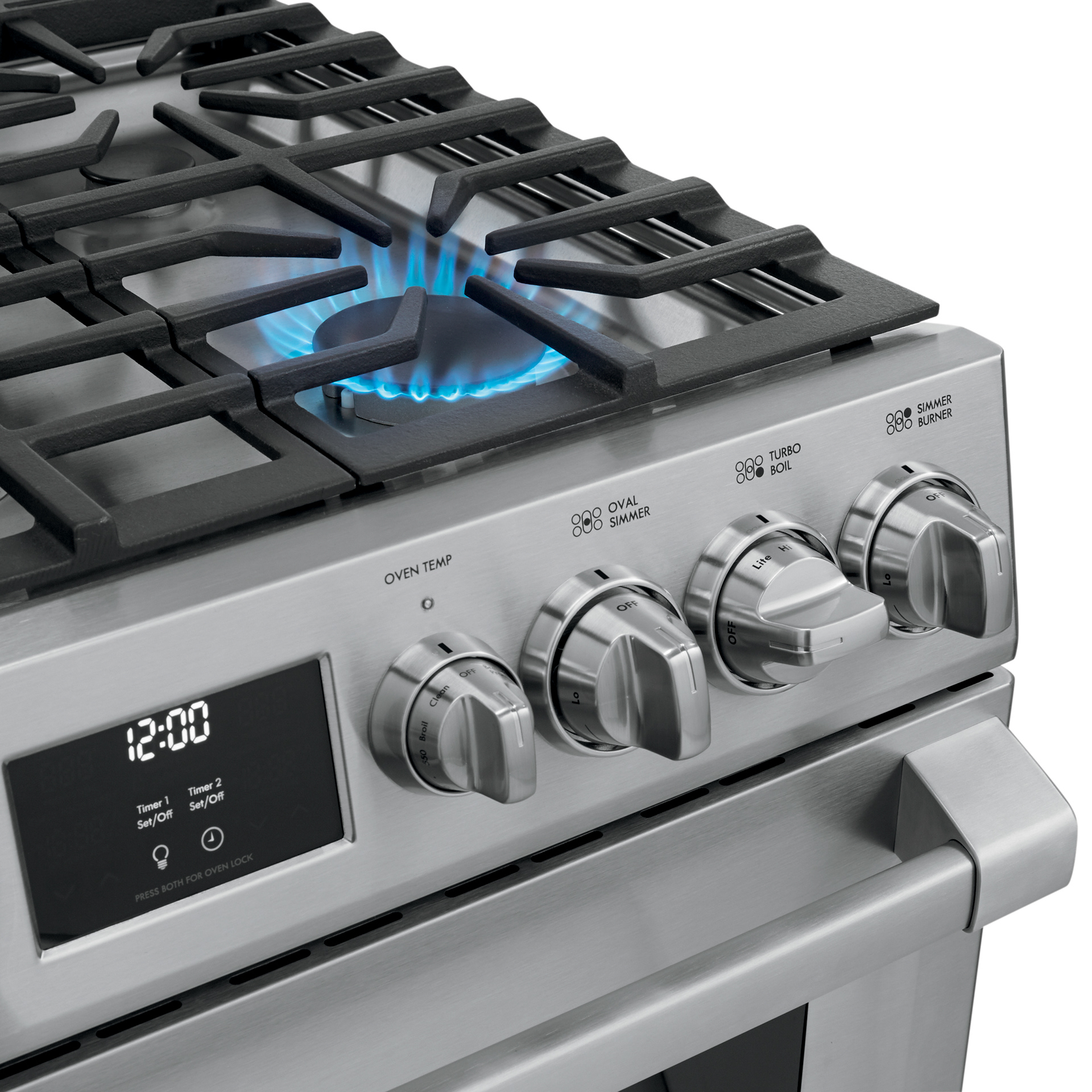
In addition to the range, the grates had to be developed for the drop-in and slide-in cooktops.
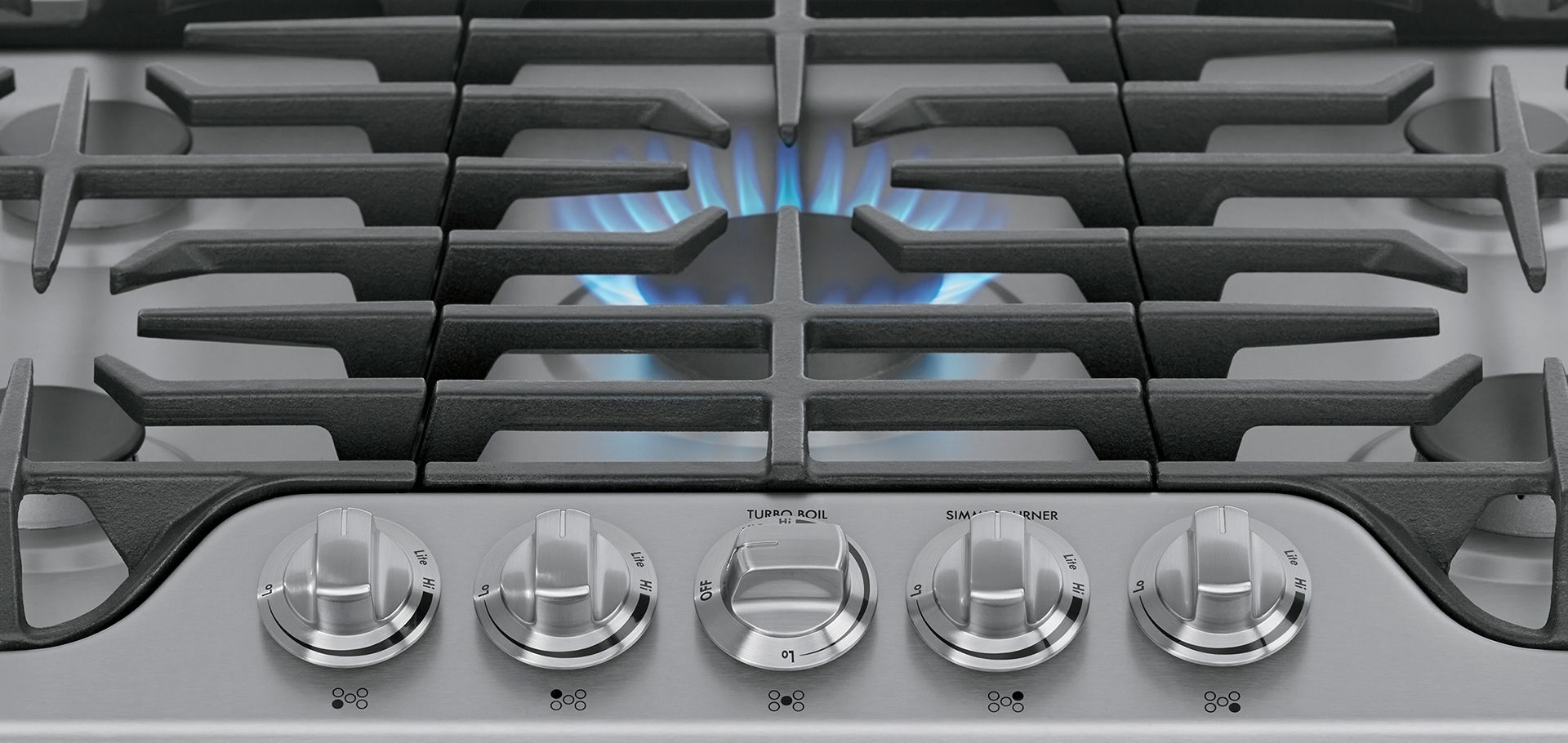
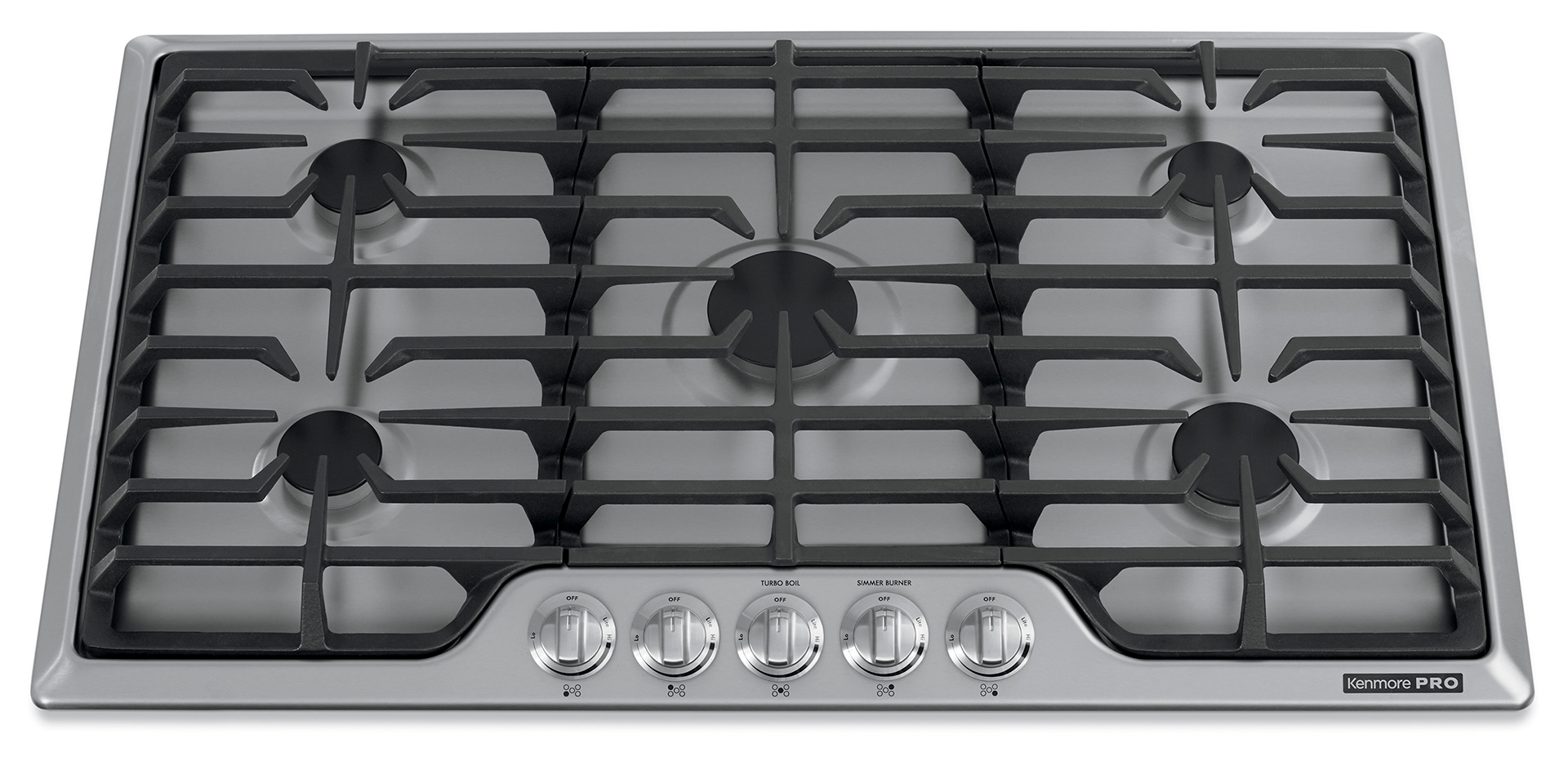
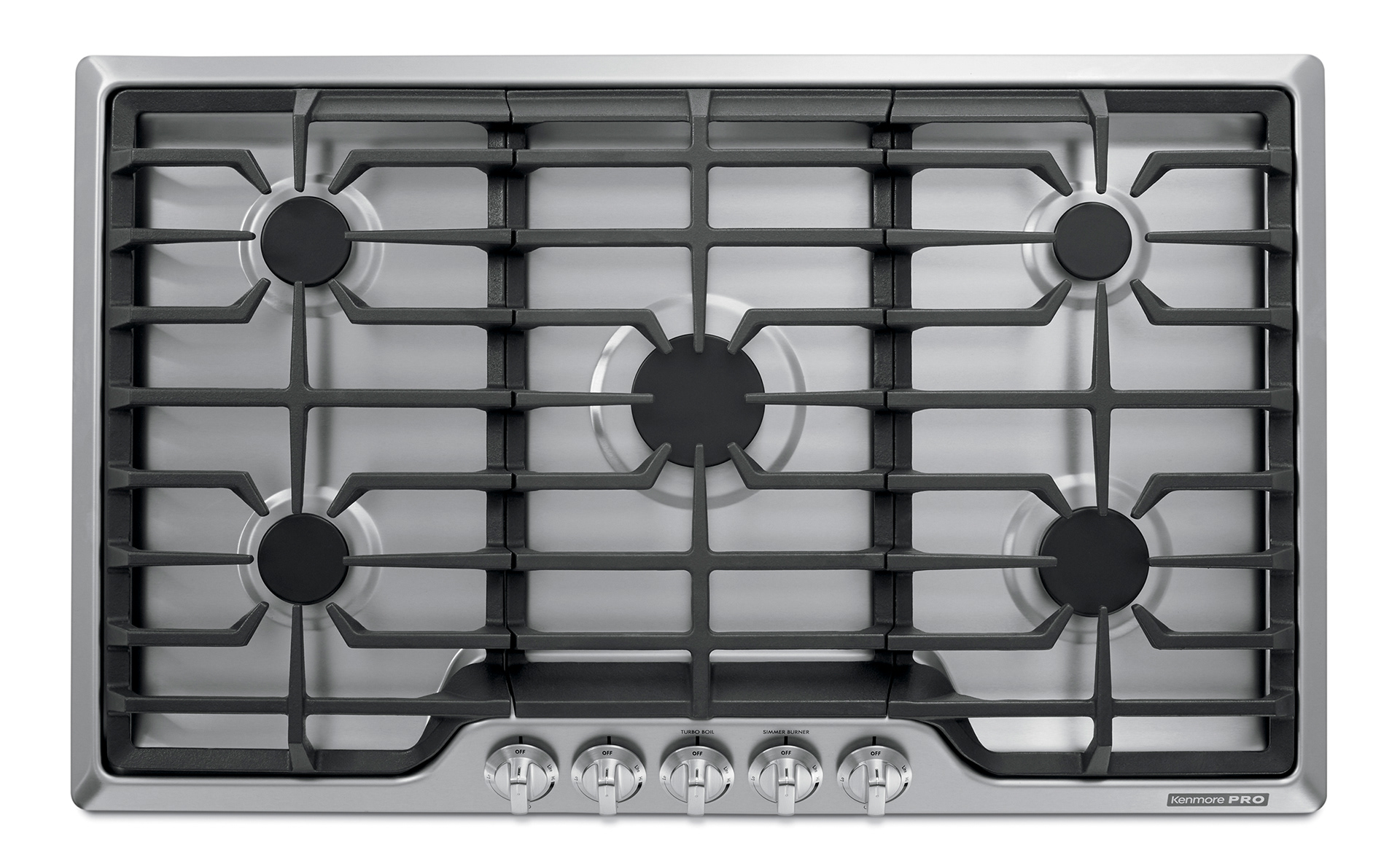
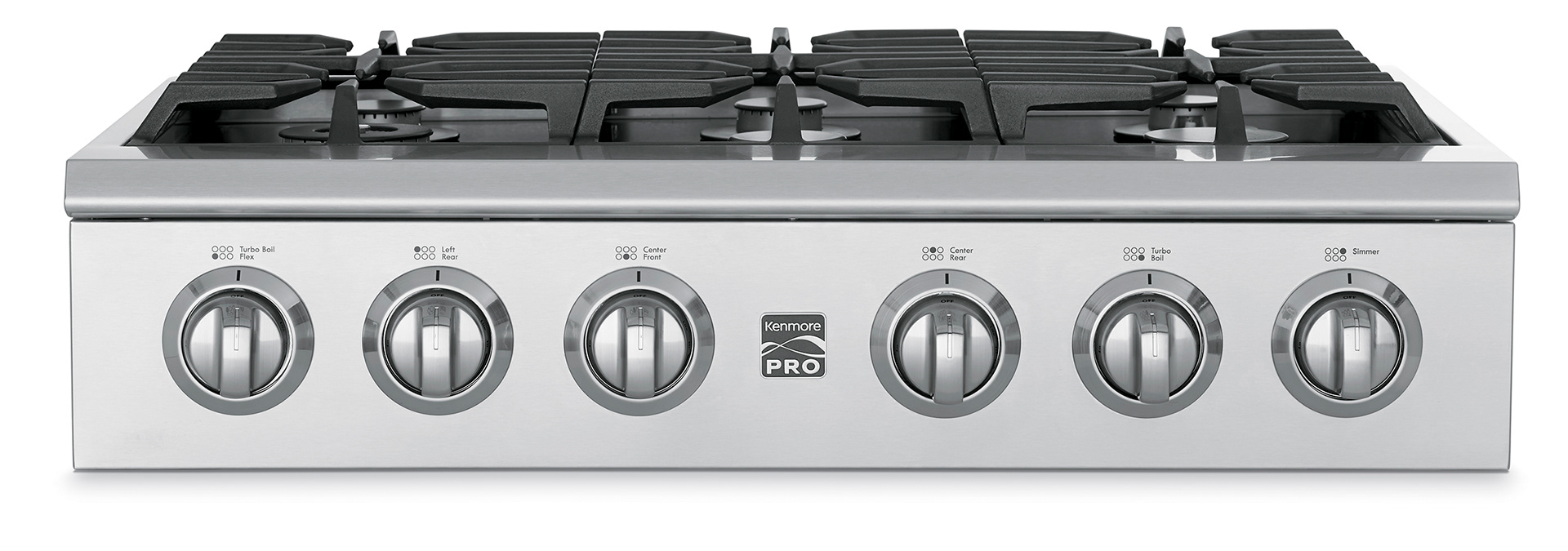
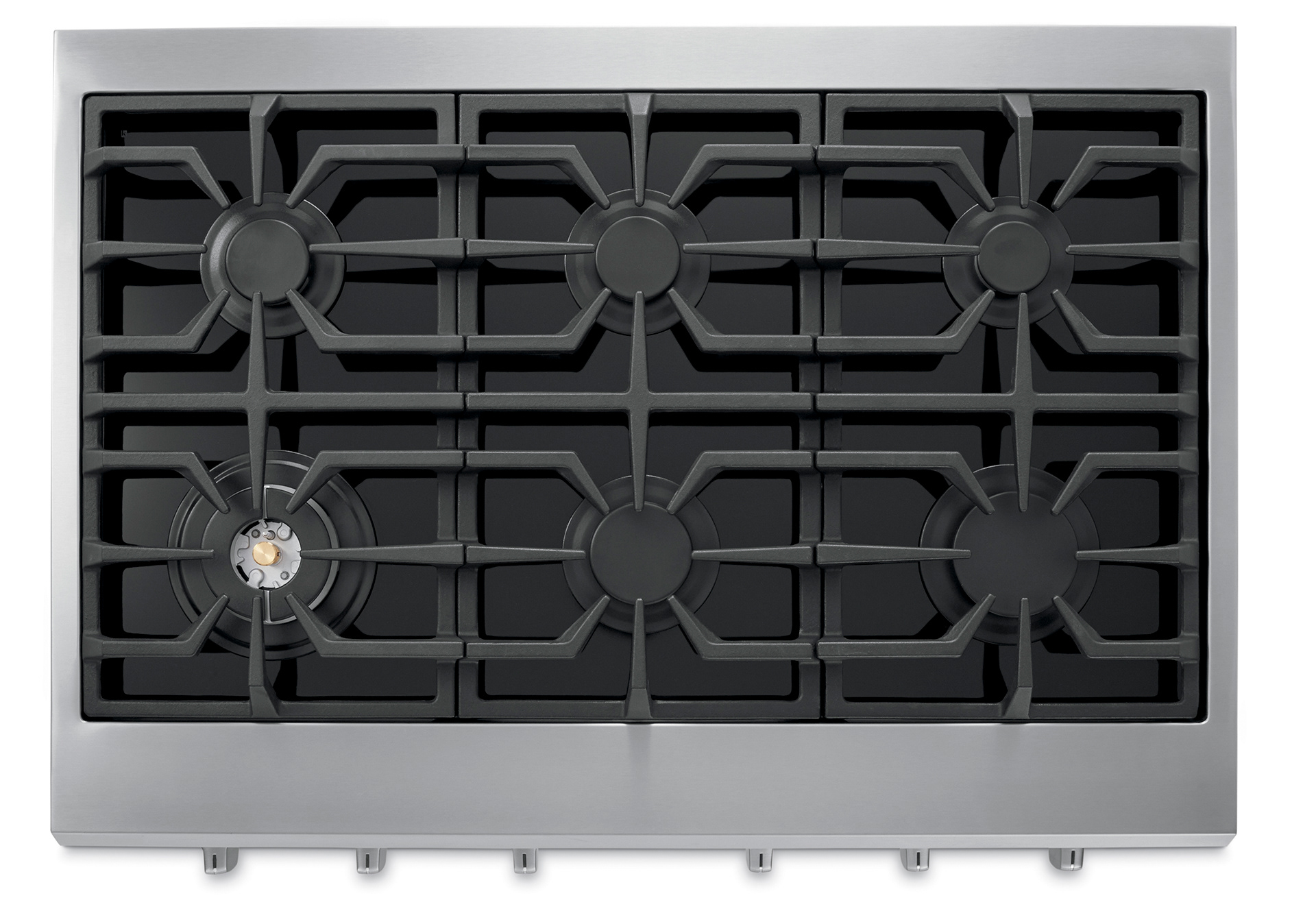

The over-the-range microwave and wall ovens were also key pieces of the product suite that I worked on.
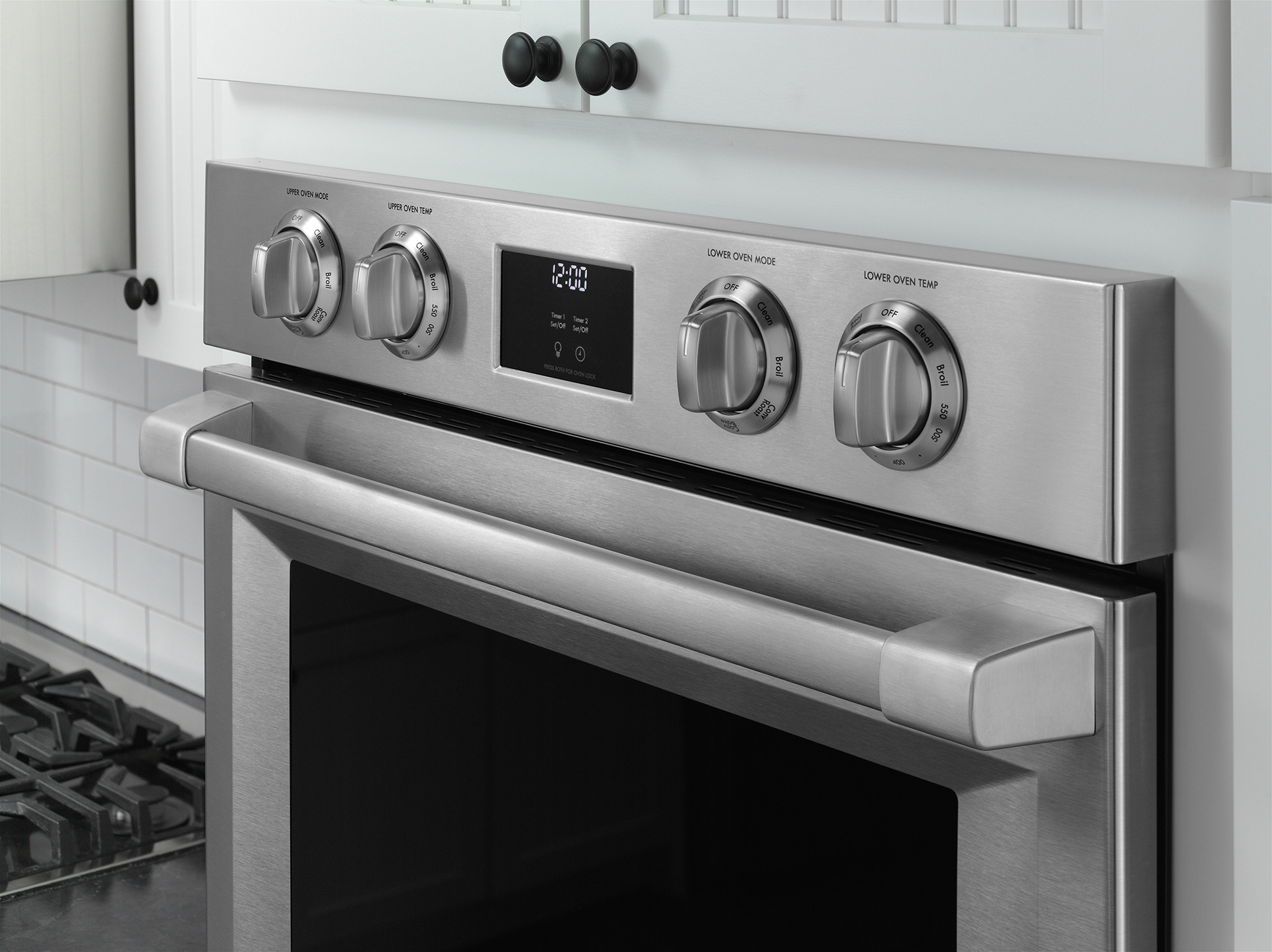

The UI for the ovens was a good story of prototyping, testing, failing, and fixing. The original concept was based on the hypothesis that 'professional' customers wanted simple analogue controls. The temperature readout was only on the knob with no display feedback. This clearly did not work for consumers, and we course-corrected to add the temperature feedback onto the control. This proves to be one of the lowest service-call-rate controls for user instruct within the company.
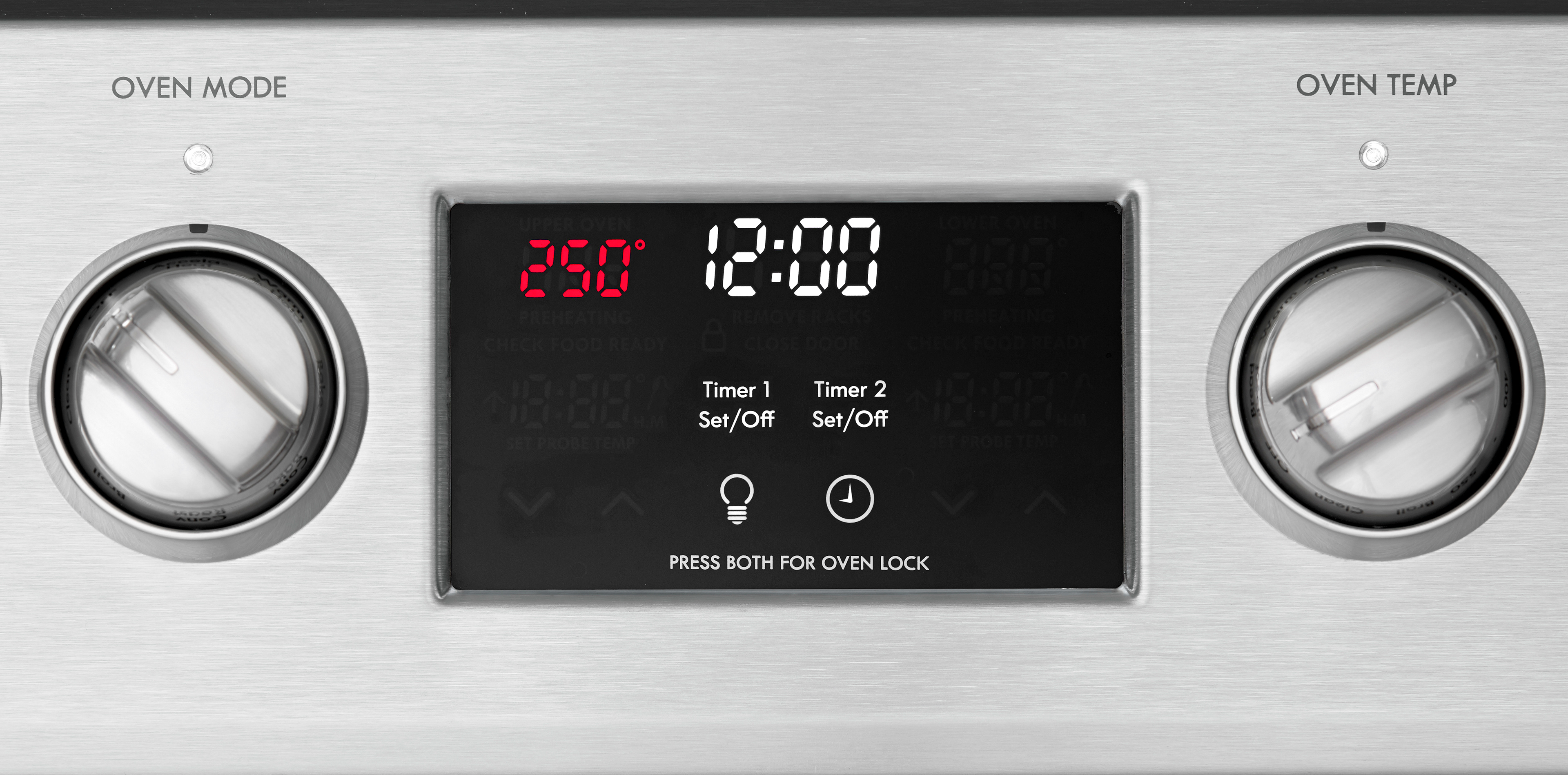